The industrial welding industry is facing a global shortage of skilled workers, with the number of welders in the UK alone having fallen by a quarter in just five years. What’s more, half of the nation’s current welders are expected to retire by 2027, creating up to 36,000 additional vacancies nationwide.
This lack of skilled welders is also exacerbating issues such as the housing crisis, as there simply isn’t enough certified talent to help build the 300,000 houses required in the UK every single year.
The good news is that Soldamatic Industrial Services are currently helping to revolutionize welding training in the UK, through the creation of digital solutions that are efficient, targeted and capable of being customized to suit specific applications.
This is especially important in the rail industry, where training the next generation of welders is crucial if we’re to ensure the safe and efficient transportation of people and goods. We’ll explore this in the article below while asking how Soldamatic’s training solution can benefit the industry.
The Importance of Railway Welding
Railways in the UK transport huge numbers of goods and passengers every single year, with 359 million passenger journeys completed in the third quarter of 2022 alone.
Incredibly, strike action by the railways unions disrupted travel for five days during this quarter, highlighting the demand that exists for rail services nationwide.
This growing demand also places a strain on the structural integrity of individual tracks, and railway welding plays a key role in maintaining this over time. This can help to prevent derailments and ensure reliable transportation, delivering significant financial and human benefits in the process.
Railways also transport goods and materials that are used in various industrial applications so maintaining these tracks with the latest welding techniques can contribute positively to the supply chain and help underpin the wider economy.
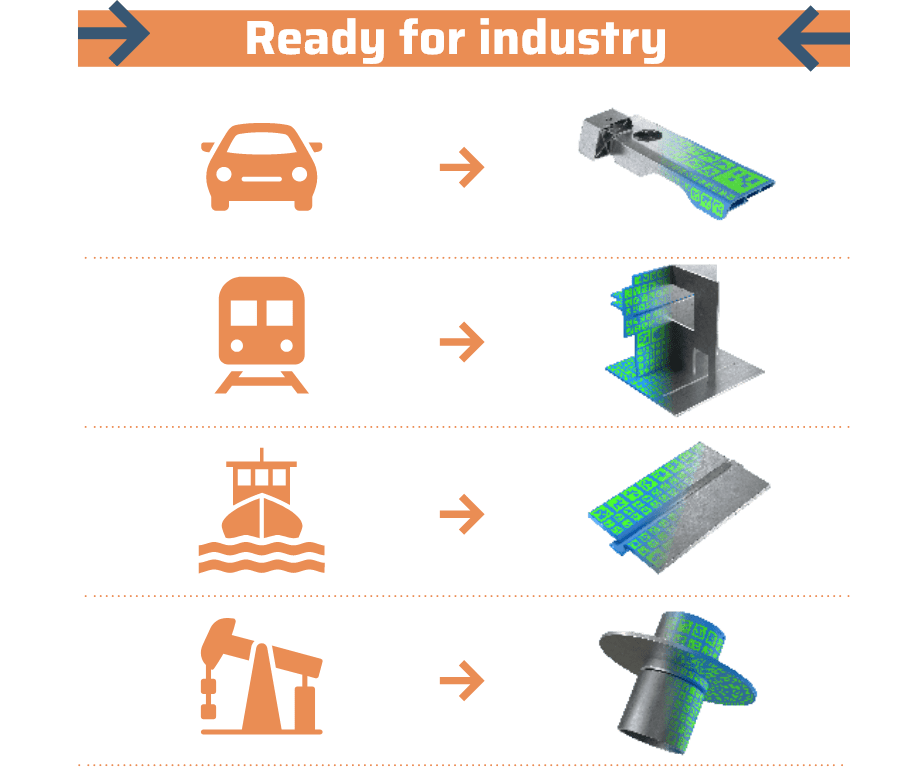
How Can Soldamatic Boost Railway Welding?
Railways clearly play a key, if often understated, role in supporting economic growth and expansion. But how can Soldamatic’s digitized training solutions help to deliver the next generation of railway welders and improve efficiency within the industry? Let’s get into it!
Effectively Imparting Safety Skills
Safety is paramount when creating and maintaining railway welding joints, especially as the tracks are constantly exposed to a combination of hazards.
These include exposure to heat and other extreme weather conditions, sparks and chemical agents, which can challenge the structural integrity of tracks over time. Welders must also be adequately trained in the proper use of personal protective equipment (PPE) to minimize their own risk, including welding helmets, safety glasses and gloves.
But how can Soldamatic’s industrial welding solution help in this respect? Well, Soldamatic’s simulations leverage augmented reality to combine corporeal hardware with advanced software, allowing people to use official welding gloves and torches and become familiar with this equipment in a completely safe environment.
Soldamatic’s safe simulation models also eliminate the risk of injury during training, while ensuring that users are taught the correct posture and body positions when welding. This reduces the cost of absenteeism over time and can translate into significant savings for companies.
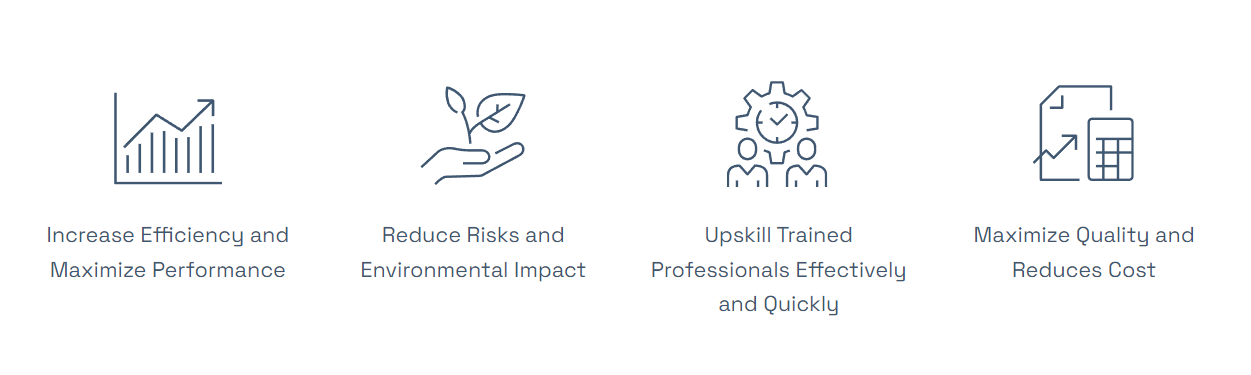
Teaching Welding Techniques
Another key consideration when training railway welders is the range of skills that they’re able to learn, as different techniques may be required depending on the precise application in question.
More specifically, workers in the field must be skilled in shielded metal arc welding (SMAW), gas arc metal welding (GMAW) and flux-cored arc welding (FCAW). They should also be trained in the proper use of additional welding equipment, including welding machines, electrodes, and welding wires, while being able to identify the different types of weld in use (such as butt, lap and fillet welds).
One of the key benefits of Soldamatic’s industrial training solution is that it can be developed to suit specific applications and needs. This means that after the precise requirements of a client have been explored and recommended solutions agreed, the process of customizing solutions and simulation parameterization can begin.
The ability to adjust and personalize parameters leads to increased efficiency when teaching multiple welding techniques. It also simplifies the process of upskilling trained professionals and imparting new techniques, enabling companies to meet the real-time demands of projects in a quick and cost-effective manner.
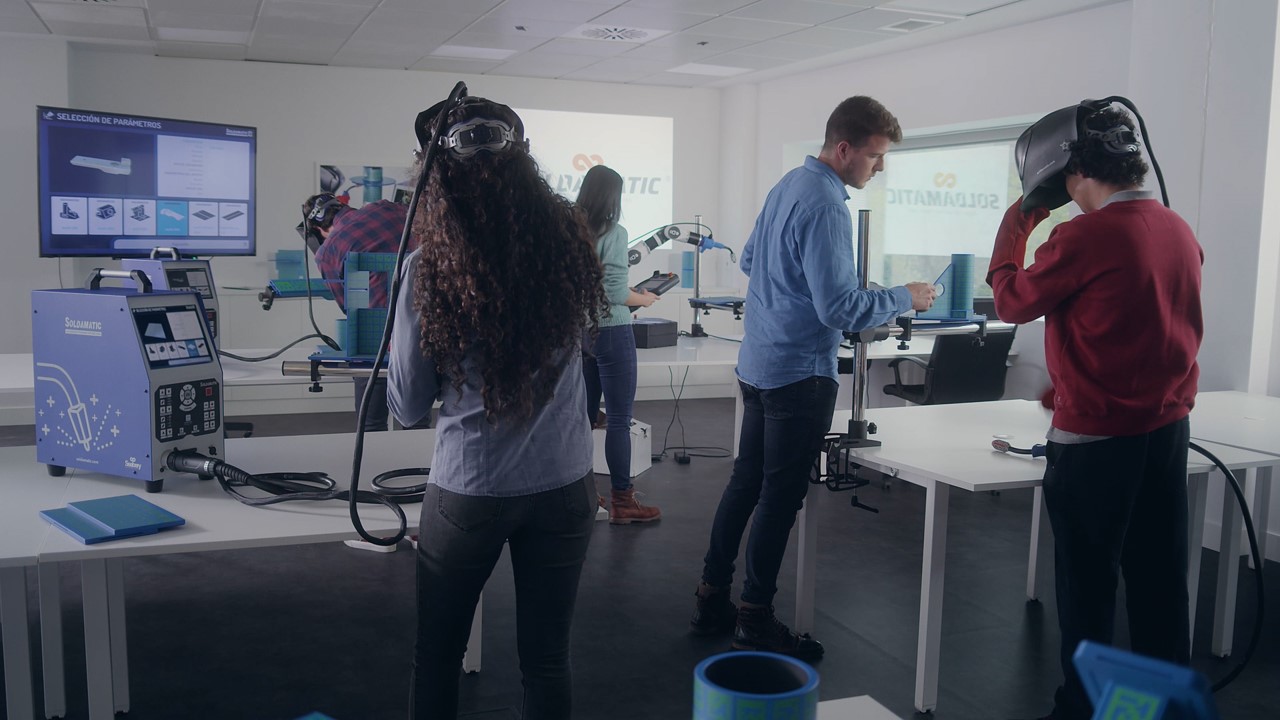
The Last Word
As we can see, Soldamatic’s industrial solutions are tailormade for the rail industry, as it enables new and experienced welders to safely practice their skills while learning about correct postures for welding.
It can also use flexible simulation parameterization to teach different welding techniques, while leveraging real-world scenarios through an augmented reality platform that combines both corporeal and virtual elements. Another key facet of the solution is that it delivers insightful feedback on welding quality in real-time, further personalizing the learning experience by identifying specific areas that need improvement.
Overall, Soldamatic industrial training solutions maximize quality and drive superior levels of knowledge retention, while reducing risk and all of its associated costs. This bodes well for the future of the railway industry, which relies on a steady supply of skilled welders to support safe and efficient travel.