Tungsten Inert Gas (TIG) welding, also known as Gas Tungsten Arc Welding (GTAW), is a versatile and highly precise welding process widely used in various industries. TIG welding offers unparalleled control, producing clean, high-quality welds. In this article, we will delve into the TIG welding process, its applications, advantages, and key considerations for achieving exceptional welds.
Understanding TIG Welding
TIG welding is a fusion welding process that uses a non-consumable tungsten electrode to create an electric arc between the electrode and the workpiece.
This arc generates the heat required to melt the base metal and form a weld. As the name suggests, an inert gas, typically argon or helium, is used to shield the weld zone from atmospheric contamination.
The lack of a consumable electrode distinguishes TIG welding from other processes like MIG (Metal Inert Gas) welding.
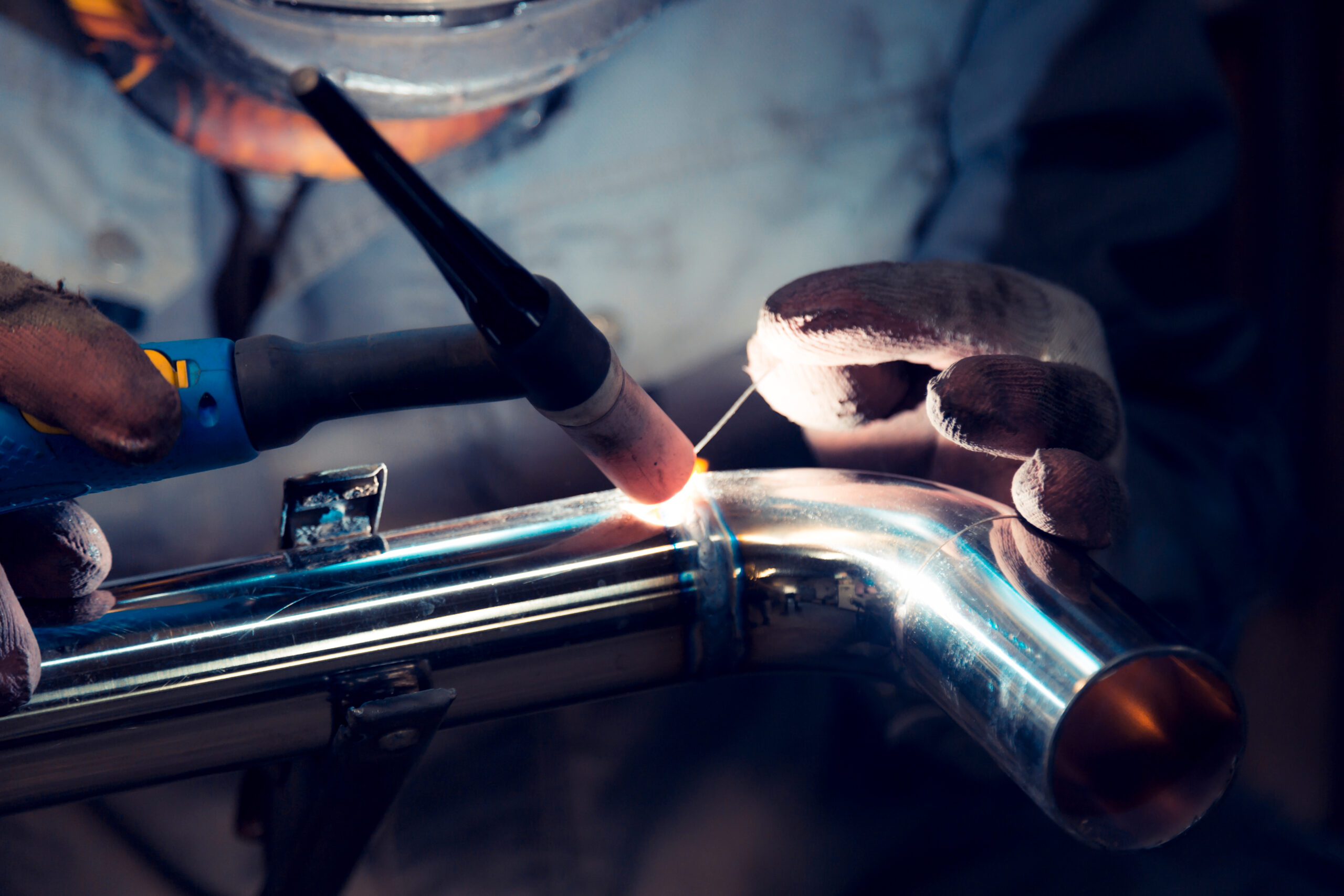
Key Components of TIG Welding
According to the TWI Global’s article, the main equipment components are:
- Power Source: A TIG welding machine generates the necessary electrical current for the welding process. It allows for precise control of the welding parameters, such as amperage and voltage.
- Tungsten Electrode: The non-consumable tungsten electrode is at the heart of TIG welding. It withstands extreme heat and does not become part of the weld. It can be either pure tungsten or contain additives like thorium, cerium, or lanthanum to enhance performance.
- Inert Gas Supply: Argon or helium is used as the shielding gas. The choice of gas depends on the specific requirements of the welding job, with argon being the most commonly used.
- Welding Torch: The torch holds the tungsten electrode and provides a means to deliver the inert gas to the welding zone. It also serves as the electrical conductor to create the arc.
- Filler Rod: In cases where additional material is needed to create the weld, a filler rod made of the same or compatible material is added manually. This is a common practice in TIG welding.
If you are interested in knowing more about generic welding equipment, we recommend you read this blog article.
Advantages of TIG Welding
It becomes evident that this process offers a multitude of advantages that distinguish it in the field of welding techniques. Its precision, versatility, and ability to produce clean, high-quality welds make TIG welding a preferred choice for various industries. According to this article, we have found these advantages:
- Versatility: TIG welding can be used to join a wide range of materials, including stainless steel, aluminum, copper, and exotic alloys. Its ability to produce clean, aesthetically pleasing welds makes it a preferred choice for industries such as aerospace, automotive, and pharmaceuticals.
- Precision and Control: TIG welding is renowned for its precision, making it suitable for intricate, high-quality welds. The welder has fine control over the heat input and can make minute adjustments to the welding parameters during the process.
- Minimal Splatter and Fumes: TIG welding produces minimal splatter and fumes, ensuring a safer and cleaner working environment.
- High-Quality Welds: TIG welds exhibit excellent mechanical properties, such as strength and corrosion resistance. This makes them suitable for critical applications.
Applications of TIG Welding
TIG welding is used in various industries and for a multitude of applications, including:
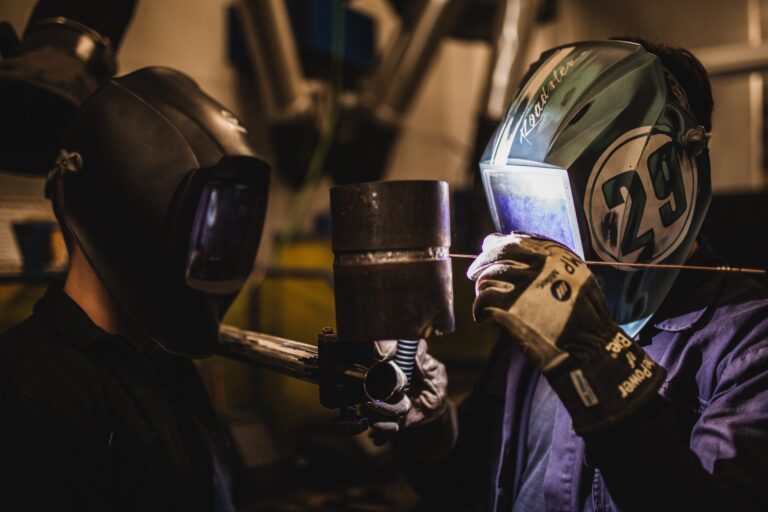
- Aerospace: TIG welding is crucial in aerospace manufacturing, where precision and quality are essential. It is used to join materials like titanium and aluminum in the construction of aircraft and spacecraft.
- Food and Pharmaceutical: TIG welding ensures the creation of hygienic and contamination-free welds in stainless steel equipment used in food and pharmaceutical production.
- Automotive: TIG welding is used to fabricate exhaust systems, body panels, and various structural components in the automotive industry.
- Art and Sculpture: Many artists and sculptors employ TIG welding for its artistic versatility and ability to create intricate designs.
- Pipe Welding: TIG welding is commonly used for welding pipes, especially in the petrochemical industry, due to its ability to produce high-quality, leak-free welds.
Considerations for TIG Welding: why is Soldamatic the Key to your Success
As we have seen, TIG welding has great benefits, but at the same time it requires an advanced level of welding for proper execution. Welders can unlock the full potential of TIG welding to achieve outstanding results in vital sectors such as aerospace and automotive by employing proper equipment, training, and meticulous attention to detail.
In this sense, Soldamatic’s Augmented Reality technology allows this complex technique to be tested without any risk for new welders, while avoiding excessive waste of materials.
By using Soldamatic you can also improve:
- Skill and Training: TIG welding demands a high level of skill and precision. Proper training and practice are essential for achieving quality welds.
- Positions: As you may know, TIG welds can be made in all positions, this is something that is also possible to train with Soldamatic. You can either practice TIG welding with the different Training Joints or show your abilities with the Advanced Welding Multijoint “Foundational Multilap” on PB position. We also recommend you check the catalogue of joints available.
TIG welding is sometimes used as a way of measuring a welder’s skill, as it is a complex process that shows how skilled and experienced the welder is. This is vital for many companies that need to hire new welders, as they need empirical evidence of the candidate’s level.
In this sense, companies like Alstom already use Soldamatic to evaluate the ability of their welding candidates, bringing real welding exercises to Augmented Reality, exactly like the ones they will have to develop in the position they are applying for. In this way they get a 100% objective analysis of their capabilities, while saving on all the materials needed to perform the exercises
Conclusion
TIG welding one of the main welding processes; it is a versatile and highly precise welding process, offering the ability to create clean, high-quality welds in a wide range of applications. With the right equipment, training, and attention to detail, welders can harness the full potential of TIG welding to produce exceptional results in critical industries like aerospace, automotive, and more.
Used for most demanding industrial applications, TIG welding combined with Augmented Reality technology of Soldamatic stands as a testament to the fusion of craftsmanship in the world of welding