Welding, an age-old technique, has played a pivotal role in the development of various industries, including manufacturing, construction, and aerospace. Over the years, the welding process has evolved significantly, with innovations in equipment and the integration of advanced simulation technologies. These developments have not only enhanced the efficiency and quality of welding but have also contributed to a safer and more sustainable welding industry. This article explores the new technologies in welding, from cutting-edge equipment to simulation tools, highlighting their impact on the welding industry.
Advanced Welding Equipment
Modern welding equipment has experienced a remarkable transformation in recent years. The integration of new technologies has made welding processes more precise, efficient, and accessible. Some key advancements in welding equipment include:
Digital Controls: Welding machines now feature digital controls that allow for precise adjustment of welding parameters, such as voltage, current, and wire feed speed. This enhances control over the welding process, resulting in higher quality welds.
Inverter Technology: Inverter-based welding machines have become increasingly popular due to their portability, energy efficiency, and improved arc stability. They enable welders to work more effectively in a variety of settings.
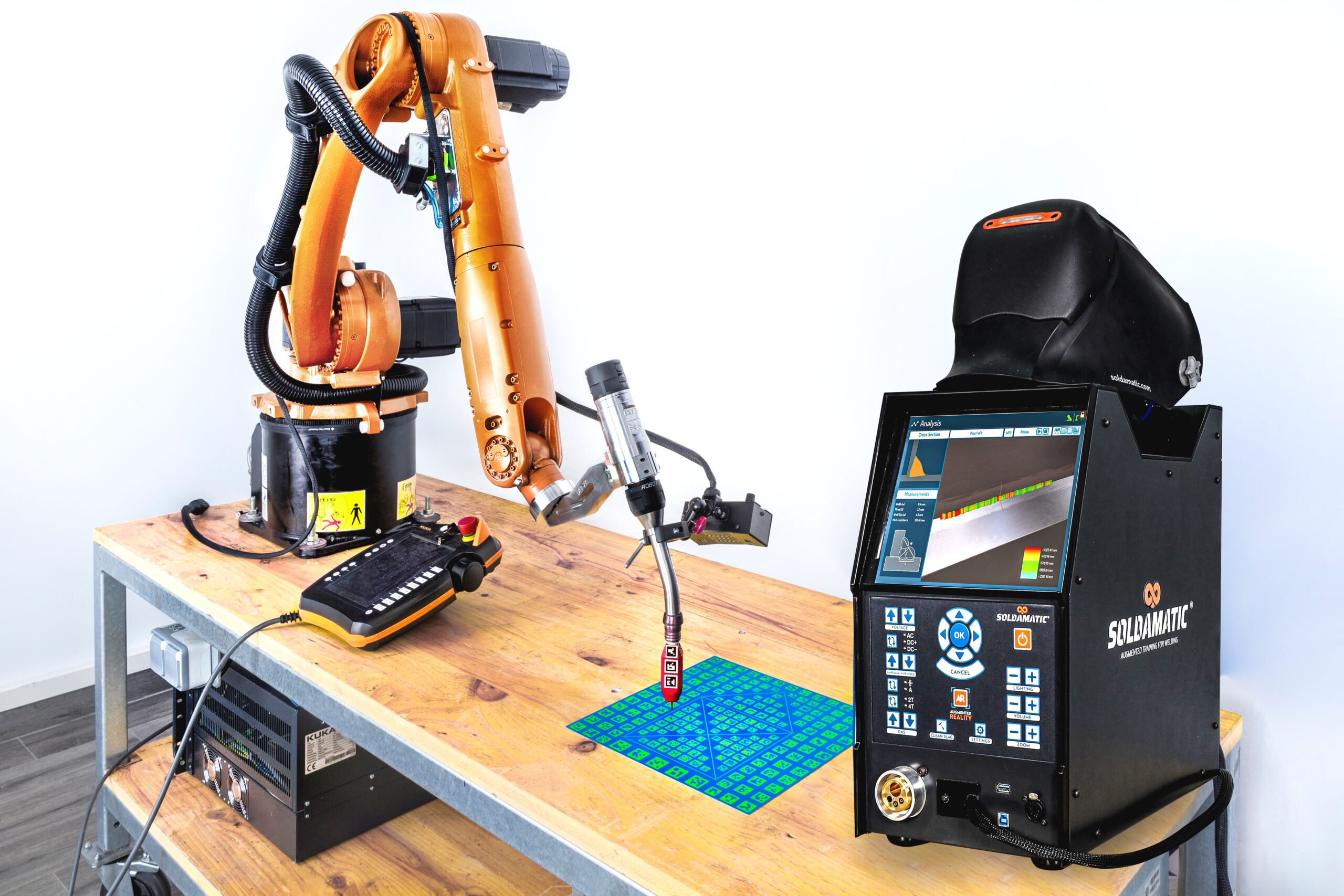
Automation and Robotics: Automation and robotics have gained prominence in welding applications, especially in industries like automotive and aerospace. Welding robots can work tirelessly, producing consistent welds with minimal error. If you want to know more about this topic, we recommend you read this article.
Laser and Plasma Welding: Advanced welding techniques, such as laser and plasma welding, offer higher precision and control, making them suitable for delicate applications like medical device manufacturing and electronics.
Virtual und Augmented Welding Simulators
Simulation technology has revolutionized welding training and education by providing a safe and cost-effective way for welders to practice and improve their skills. Virtual welding simulators have gained popularity for several reasons:
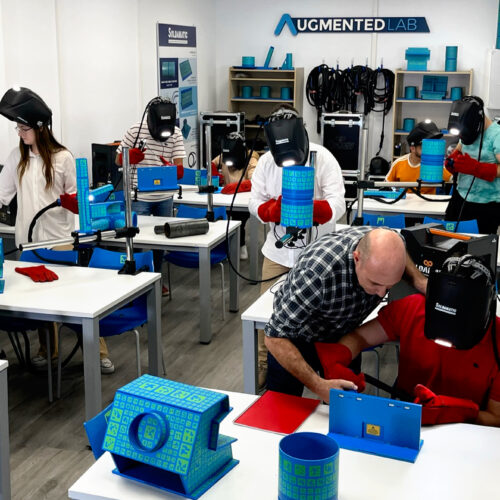
- Safe Learning Environment: Virtual welding simulators eliminate the risks associated with live welding, including exposure to harmful fumes and the potential for accidents. This promotes a safer learning environment for novice welders.
- Cost-Efficiency: Traditional welding practice involves consuming materials and energy, which can be expensive. Simulators reduce these costs by using virtual materials, making it more affordable for training programs.
- Realistic Feedback: Simulators provide immediate feedback on welding performance, allowing users to identify and correct errors in real-time. This accelerates the learning curve and improves skill development.
- Customized Training: Virtual welding simulators offer various welding scenarios and difficulty levels, catering to the needs of both beginners and experienced welders. They can simulate different welding processes, materials, and joint configurations.
Augmented Reality (AR) in welding: Soldamatic Augmented Training
Augmented Reality technologies are making their way into the welding industry, offering exciting possibilities for training, design, and inspection:
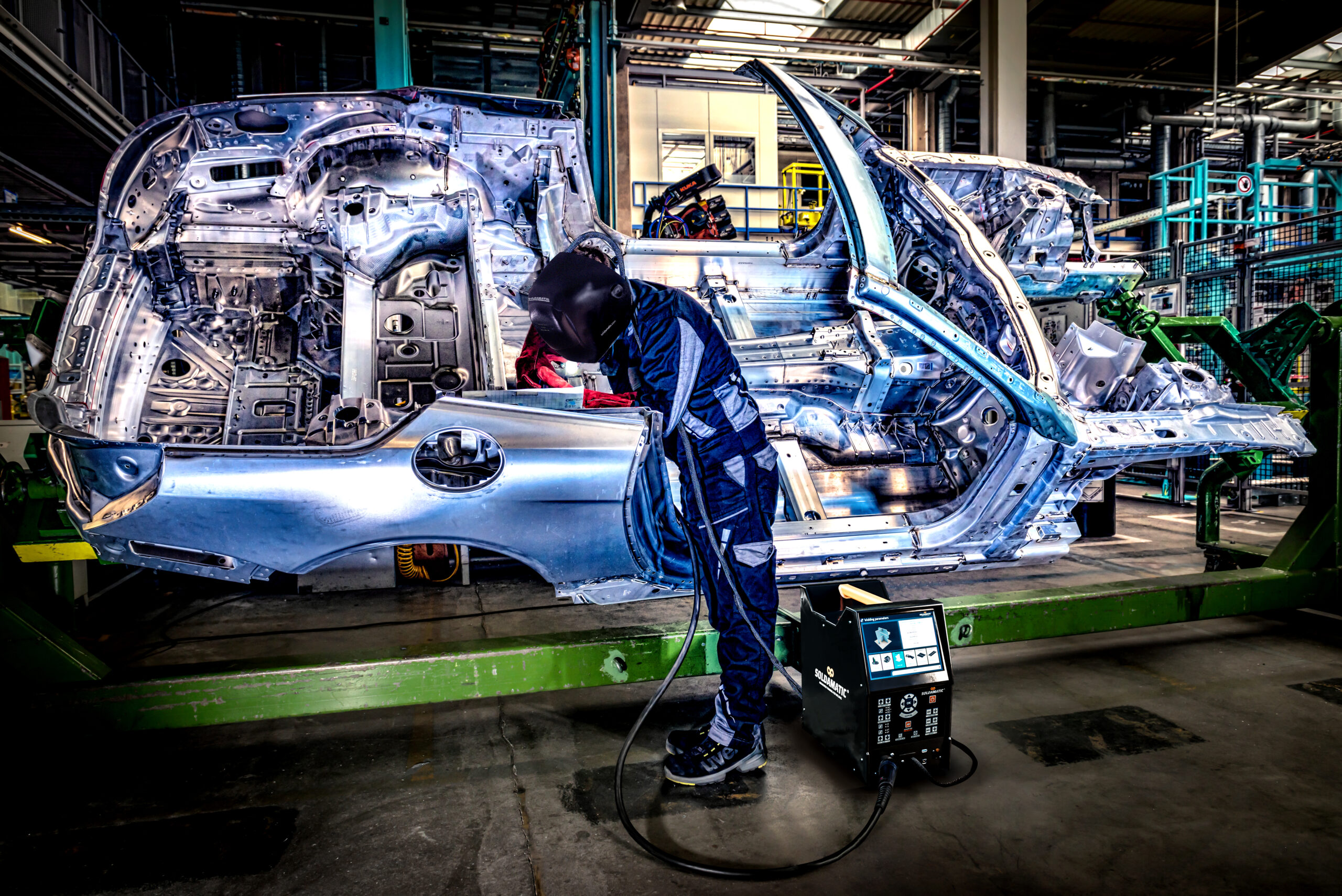
Training Enhancement: AR can provide immersive welding training experiences, where users can practice welding techniques in simulated environments. These technologies offer a more interactive and engaging learning experience. Many training centers and welding schools often use these welding simulators in their programs.
Design and Planning: Engineers and designers can use AR to visualize weld joints and welding sequences in three-dimensional space. This aids in better design and planning of welding projects, reducing errors and rework.
Remote Inspection: Augmented Reality allow experts to remotely inspect welds in real-time, providing guidance to on-site welders. This reduces the need for physical presence at job sites, saving time and resources.
Soldamatic combines all these technological advancements not only improving the quality of welds but also contributing to a safer and more sustainable welding industry. It allows an immersive training while reducing costs and possible injuries. Soldamatic is a practical example of how AR technology has been integrated into the welding industry.
The future of new welding technologies is now
The welding industry has come a long way with the integration of new technologies in both equipment and training. As technology continues to evolve, it is imperative for welders and welding companies to embrace these innovations to stay competitive and deliver high-quality products and services. Advanced welding equipment enhances precision and efficiency, and Soldamatic provides innovative solutions for welding projects.